2304 Stainless Steel Introduction
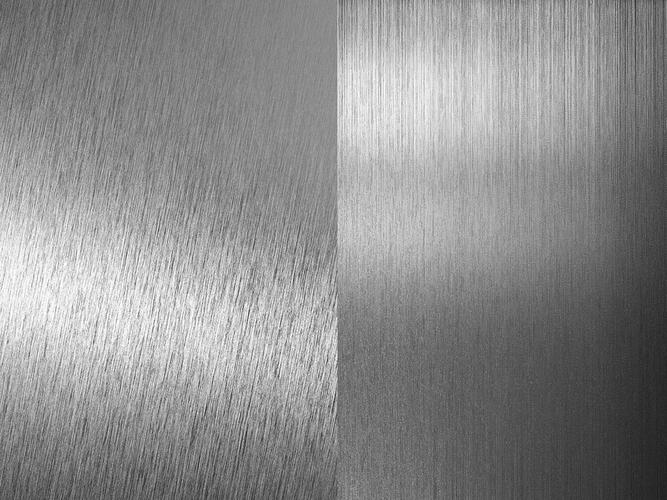
Alloy 2304 is a compound stainless steel consisting of 23% chromium and 40% nickel. 2304 alloy has corrosion resistance properties similar to 316L. In addition, its mechanical properties such as compressive strength are twice that of 304/316 austenitic grades. This property is the designer can design to reduce the weight of the product, especially in the design of pressure vessels.
This alloy is particularly suitable for the -50°C/+ 300°C (-58?/572?) temperature range. It can also be used at lower temperatures under severe restrictions (especially for welded structures).
The lower nickel content and higher chromium content of alloy 2304 make it more resistant to stress corrosion than 304 and 316 austenitic due to its inherent complex microstructure.
Application areas
1)Most of the fields used in 304 and 316
2)Pulp and paper industry (chip and debris storage tanks, black or white liquid tanks, sorters)
3) Caustic alkali solutions, organic acids (SCC resistance)
4)Food industry
5) Pressure vessels (weight reduction)
6) Mining industry (abrasion/corrosion) standards
ASTM/ASME...A240 a UNS S32304
EURONOBaM...1.4362 a X2 Cr N1 23.4
AFNOR...Z3 CN 23.04 Az
DIN ...W...Nr 1.4362
Corrosion resistance
General corrosion
Because of its high chromium content (23%), alloy 2304 is almost as resistant to corrosion as 316L.
Local corrosion resistance
The 23% chromium and 0.1% nitrogen content gives 2304 compound stainless steel superior resistance to pitting and crevice corrosion compared to 316L.
Stress corrosion resistance
Stress corrosion resistance tests conducted in aqueous chloride solutions ((8ppm 02) PH=7, >1000h) prove that 2304 has higher stress corrosion resistance than 304L and 316L due to its higher chromium content and lower nickel content.
Other anti-corrosion properties
2304 alloy compound stainless steel has passed most of the standard Ic test procedures, such as ASTM, A262E and C tests.
It has a higher corrosion rate than 316L in 65% boiling nitric acid. Due to its high yield strength, this alloy is well suited for abrasive and corrosive environments.
Chemical composition analysis
C Cr Ni Mo N Others
0.02 23 4 0.2 0.1 S=0.001
PREN(Cr%)+3.3(Mo%)=16(N%)>24
Structure
The chemical composition of 2304 was analyzed in an idealized state to obtain a 50/50 microstructure after solid solution annealing at 9507°C/10507°C (17427?/19227?).
The microstructure of 2304 is more stable compared to the molybdenum-containing complex stainless steel. The metallic phase appears only after 10 hours of holding in the temperature range of 7507°C/ 8507°C (13827?/15627?). The copper element in alloy 2304 increases the hardness of the steel after heat treatment in the temperature range of 3507°C/ 5000°C (6627?/9327?).
Hot forming
Hot forming must be carried out in the temperature range 1150/9007C (2100/16507F). After forming, a solution annealing treatment at 9507/10507 C (21007/16507F) is recommended to restore the corrosion resistance and mechanical properties. Care must be taken to avoid creep during heating of the product.
Cold forming
Cold forming of 2304 alloy is not very difficult, and cold forming equipment for 304L and 316L is also suitable for 2304, which requires high pressures for cold forming due to its high mechanical properties, including yield strength. Finally, solution annealing is recommended to restore its mechanical properties and corrosion resistance, as with hot forming.
Rust removal
The solutions and pastes used are the same as for 304L/ 316L. Due to its corrosion resistance, the pickling time is a little longer than for austenitic grades.
Machinability
In terms of drilling, 2304’s compound construction is more machinable. Its performance is comparable to that of 316LEZ*. In addition, 2304 has greater corrosion resistance and cleanliness without the need for elemental sulfur. Localized corrosion resistance is also greater. It has better machinability.
Welding
*2304 alloy can be welded with the following equipment: , .
*TIG, manual and automatic
*PLASMA, MIG, SMAW, SAW,FCAW
*Compound microstructure makes it insensitive to thermal cracking.
*The welding parameters are ideally controlled at 20-70% of ferrite composition. In order to achieve the best results, we must take into account the thickness of the product and the welding equipment (consultation is necessary). We do not recommend pre or post weld heat treatment, a complete solution annealing heat treatment can be considered.
Comments are closed.